The following is a look behind the scenes of how a custom ring is made.
I will start by showing a picture of the finished ring and then explain how the ring is made and show some of the steps in the process.
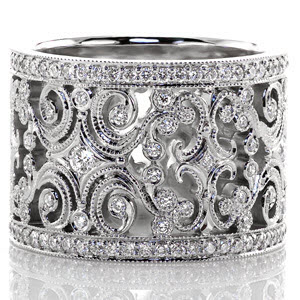
Now I will show and explain in a very condensed manner the process of making a ring like this.
Here is the ‘screenshot’ from our 3-D design software showing the design from several different angles. A design like this can take many hours of design and engineering time.
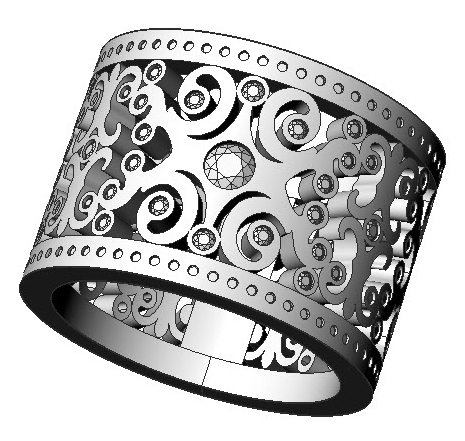
After using a CAM technology to make a physical prototype and mold used to make this ring, the design are cast in 18 karat white gold. Here is a picture of the raw castings:
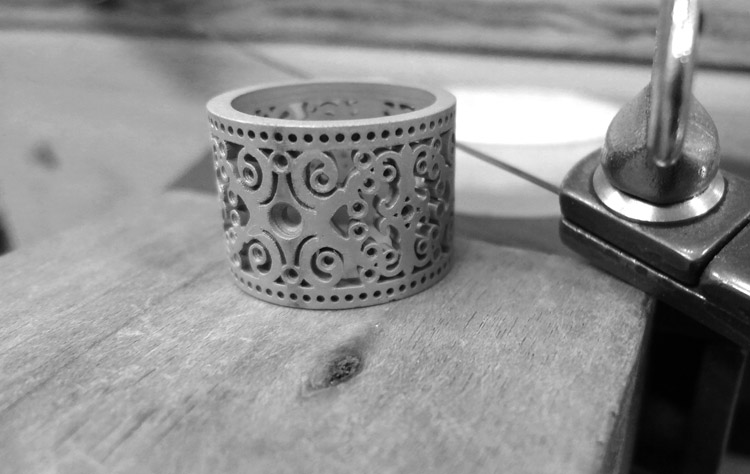
The design has three sections, the two outside rails and the inside pattern.
The overall finished width will be 15mm. Finger size 5.25
After cleaning up the raw castings ( removing sprues, smoothing, etc) the three sections are ready to finish.
Here are a couple pics after we finished setting the diamonds in the two outside rails.
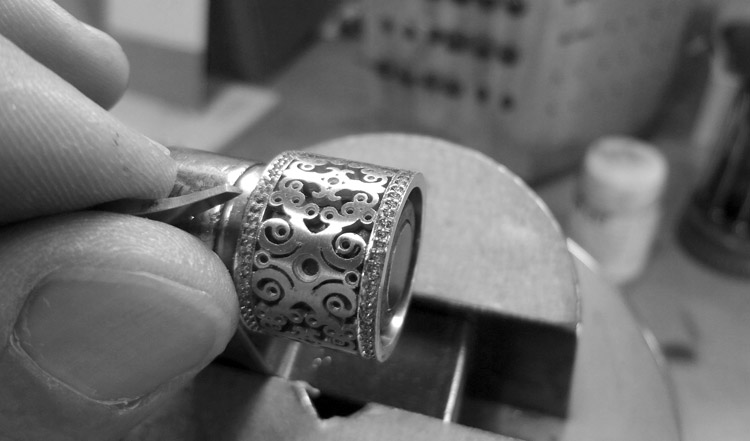
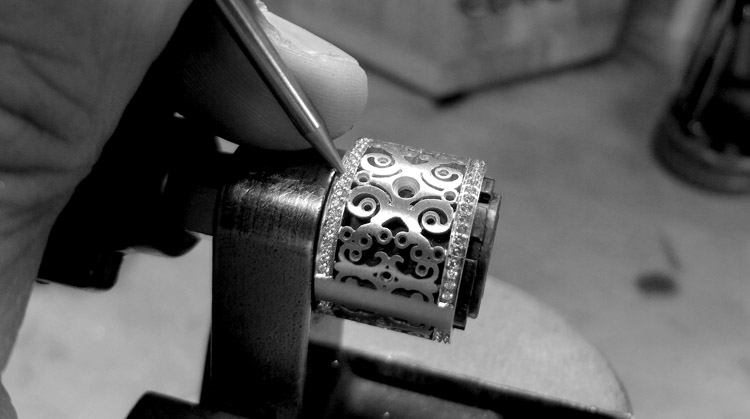
Here are a couple quick pics with the rest of the diamonds set.
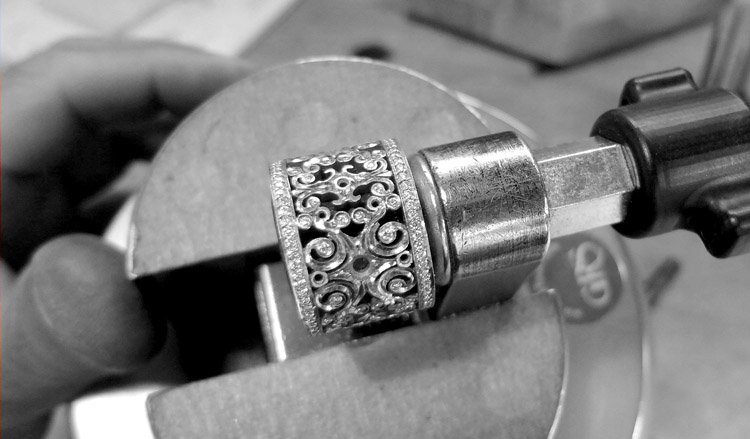
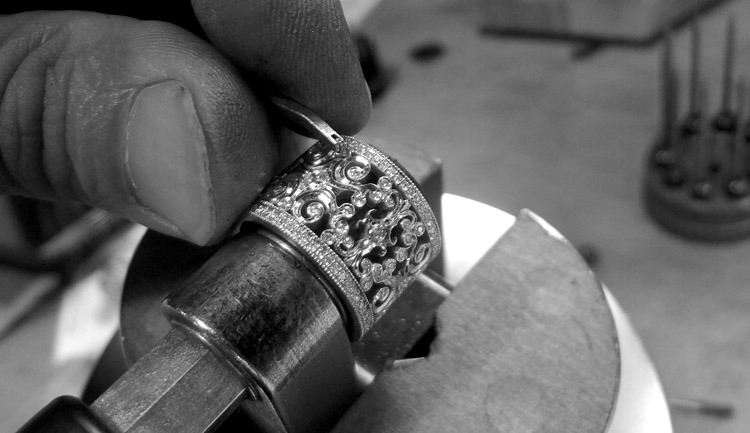
There is No Short Cut to Quality
The work necessary to obtain an immaculate look on a design with this level of detail is a very time consuming task and as we are fond of saying at Knox Jewelers, “there is no shortcut to quality”.
A master level artisan must carefully bright cut and engrave all of the beautiful detail into the areas around the diamonds and finally apply the milgrain which gives the design a beautiful and finished look.
The diamond setting, engraving and milgraining labor (not counting design work, prototyping, casting) for a ring with this level of detail will have approx 32 man hours of labor when finished.
We think of projects like this as a miniature work of art with our name on it.
Click Here to See the product page of the Finished Ring and Hi-Def Video
Please Visit our website KnoxJewelers.biz